У области модерне индустријске производње, ласерско заваривање, као високу прецизност и технологију заваривања високе ефикасности, прима све веће пажње. За потенцијалне купце ручних ласерских заваривача, разумевање разлика у ласерском заваривању различитих челичних материјала је пресудно за постизање идеалног ефекта заваривања и обезбеђивање квалитета заваривања.
Прво, упознајмо обичне челичне материјале, попут угљеничног челика, нехрђајућег челика и легура челика.
Царбон Стеел је један од најчешћих челичних материјала, а његови различити садржаји угљеника утицаће на њен рад. Ниско-карбонски челик има добру заваривост. Средњи карбонски челик захтева опрезније руковање током заваривања, док је високо-карбонски челик теже заварити.
Нерђајући челик има добру отпорност на корозију и отпорност на оксидацију. Уобичајене врсте укључују аустенитни од нехрђајућег челика, феритни од нехрђајућег челика и мартензитни од нехрђајућег челика. Њихов састав и микроструктуру одређују своје карактеристике заваривања.
Легура челика је врста челика која добија специфична својства додавањем легирских елемената, попут снаге, жилавости и отпорности на хабање.
Ласерски заваривање има опсежне примене и значајне предности на овим различитим челичним материјалима. Његова висока прецизност може постићи веома мале ширине и дубине заваривања, чиме се смањују зона погођене топлотом и побољшању квалитета заваривања. Висока густина енергије омогућава брзу брзину заваривања и увелико побољшава ефикасност. Штавише, заваривање ласерских заваривања је прелепо и има велику чврстоћу која може да испуни различите строге индустријске захтеве.
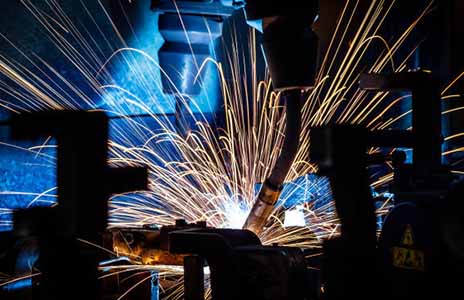
Затим се усредсредите на упоређивање и анализу кључних разлика различитих челичних материјала током процеса ласерских заваривања.
У погледу дистрибуције температуре, угљени челик има релативно високу топлотну проводљивост, тако да се топлота брзо преноси и дистрибуција температуре је релативно уједначена. Међутим, нерђајући челик има нижу топлотну проводљивост и склони се стварању локалних високих температура током заваривања, захтевајући прецизније контроле.
Ситуације деформације такође се разликују. Генерално гледано, деформација угљеног челика је релативно мала, док нехрђајући челик, због свог већег коефицијента топлотне експанзије, склон је већој деформирању током процеса заваривања.
У погледу промена композиције, током процеса заваривања легура челика, дистрибуција и губитак смањења легираних елемената имаће важан утицај на квалитет заваривања.
За различите челике, ево неких оптималних параметара ласерских заваривања и техничких сугестија.
За карбонски челик може се усвојити већа брзина заваривања и умерена ласерска снага да би се смањила улаз топлоте и избегавање прекомерног заваривања.
Нехрђајући челик захтева нижу брзину заваривања и већу снагу. Истовремено, обратите пажњу на употребу заштитног гаса како бисте спречили оксидацију.
Параметри заваривања легура челика потребно је подесити у складу са специфичним легалним саставом како би се осигурала јединствена дистрибуција легирских елемената.
Закључно, ласерско заваривање има широке перспективе у преради челика. Присуство ласерских заваривања може се видети на пољима као што су производња аутомобила, ваздухопловна, електронска опрема и медицински уређаји.
На пример, у производњи аутомобила, ласерски заваривање се широко користи у вези са структурама каросерије возила, побољшавајући снагу и сигурност тела возила. У пољу ваздухопловства, за заваривање челичних компоненти високе чврстоће, ласерски заваривање може осигурати високу прецизност и квалитет.
Да бисте вам омогућили да стекнете боље заваривање резултата у стварним операцијама, препоручујемо вам да користите наше [бренд] Хандхелд Ласер заваривач. Има напредну ласерску технологију, стабилну перформансе и практично деловање и може да задовољи ваше потребе за заваривањем за различите челичне материјале. Без обзира да ли сте мала постројења за прераду или велико производно предузеће, наш производ ће бити моћан асистент за побољшање квалитета и ефикасности заваривања.
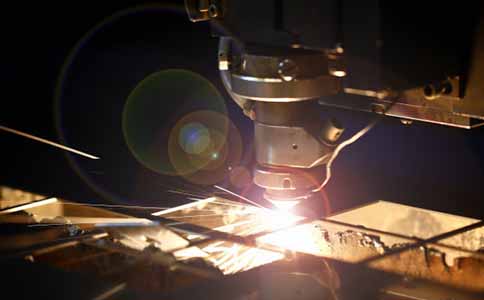
Вријеме поште: Јун-26-2024